Services
Hoctor Refrigeration offers an excellent back up service. We have a team of qualified engineers, who operate 365 days a year.
We offer maintenance contracts to suit all clients, in order to ensure that all equipment gives optimum performance and efficiency by implementing regular maintenance checks. We have a dedicated team of engineers on hand to look after our clients.
Our design team will assist in designing projects for many different types of applications. We will partner our clients to develop the system that best suits their needs and budget, while also ensuring best value for money. Our company will work with the client from start to finish to ensure the project is both energy efficient and sustainable going forward.
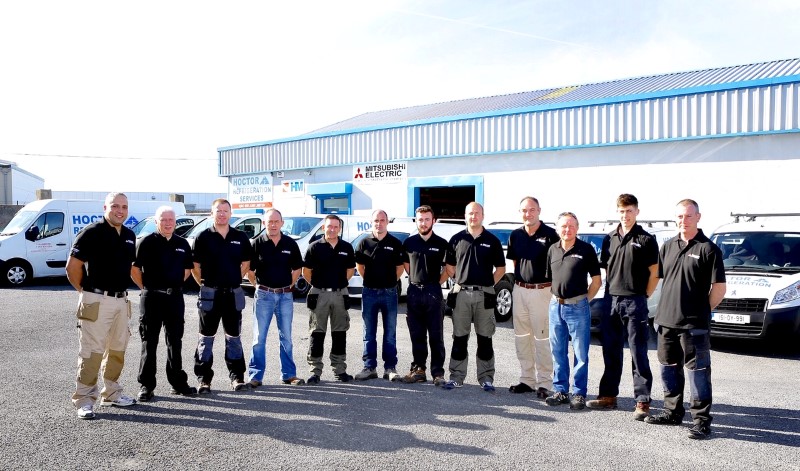
Our Engineers
Engineers
All our Engineers are apprentice trained and time served engineers. They are constantly upskilling, in order to keep pace with the changes and technical advances within the industry.
Hoctor Refrigeration is registered with;
- The IRI – Institute of Refrigeration
- EPA – PAN – Prior Annual Notification
- F-Gas Registration
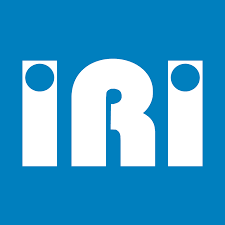
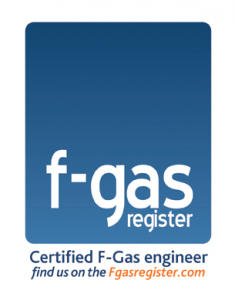

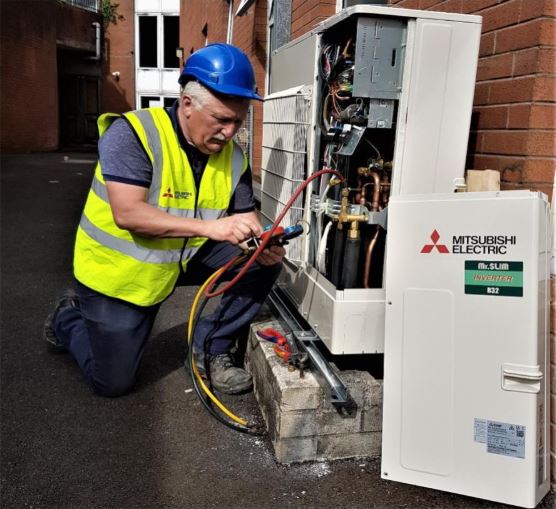
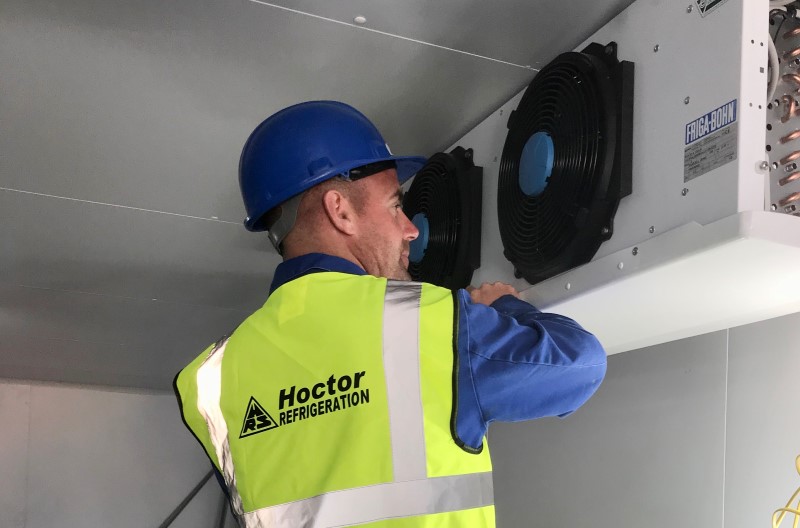
All of our staff are trained in all aspects of health and safety as it relates to their work, this training includes:
- Solas (previously Fas) Safe Pass
- Forklift Operator’s License
- Manual Handling Training
- Fire Safety Training
- Abrasive Wheels
- Harness
- MEWPs – Mobile Elevated Working Platform
- Confined Space
- Working at Heights
- Mobile Access Tower
- Refrigerant Handling to City & Guilds 2078/79
HM Maintenance Ltd.
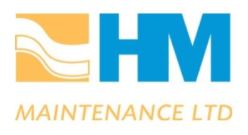
Hoctor Refrigeration have a separate company who are dedicated completely to preventive maintenance called HM Maintenance Ltd.
We offer maintenance contracts to suit all clients to ensure all equipment gives optimum performance and efficiency by implementing regular maintenance checks. HM Maintenance have a dedicated team of engineers on hand to look after our clients who have maintenance contracts with us.
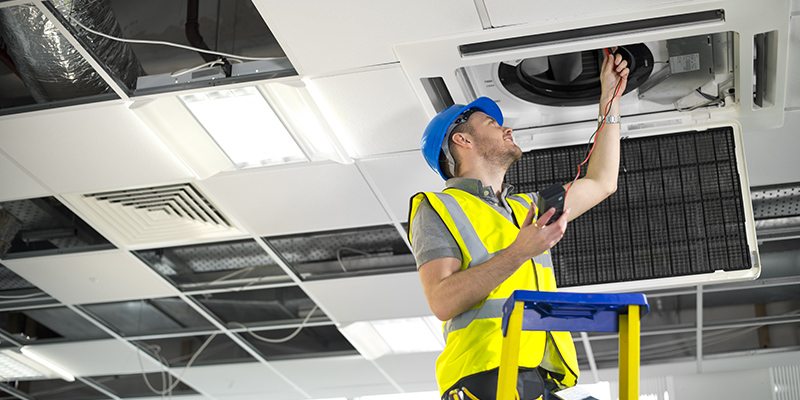
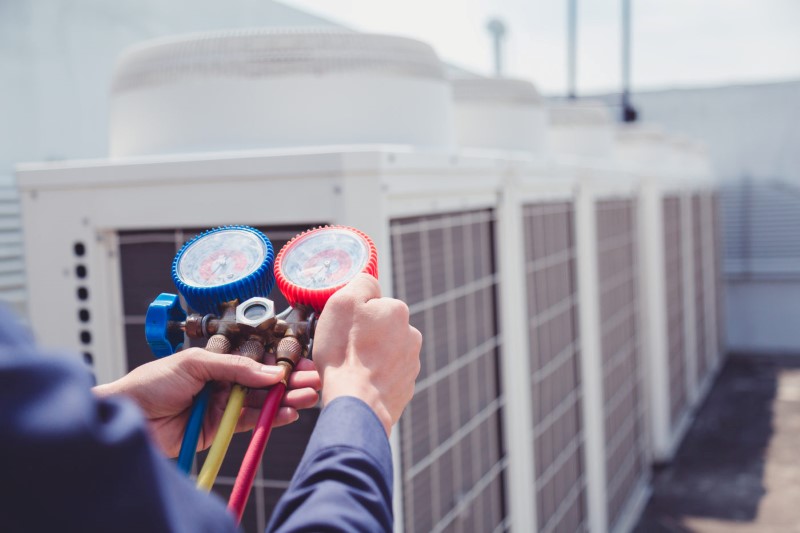
These engineers are consistently, and regularly visiting sites in a planned and scheduled way throughout the year in order to carry out tasks such as:
- Condenser Fan and Condenser Checks – These Ensure that Good Air Circulates taking place, so Ideal Heat Rejection is being provided.
- Checking Compressors are Running as Intended and as Designed.
- Carrying out Refrigerant Leak Tests and Making Sure that Repairs are Carried out in a Swift and Prompt Manner.
- Keeping Records of all Gases Used by the Systems in Accordance with the F-Gas Regulations, as well as the ODS Regulations.
- Checking Systems Controllers are set Correctly
- Making Recommendations to the Owners and Managers of Systems in an Effort to Improve System Performance and Lower Running Costs.
Regular Maintenance is designed to:
- Reduce the possibility of breakdown
- Reduce utility and repair bills
- Fast and effective breakdown service
- Competitively priced packages
- Regulator compliant
- Ensure longer equipment life
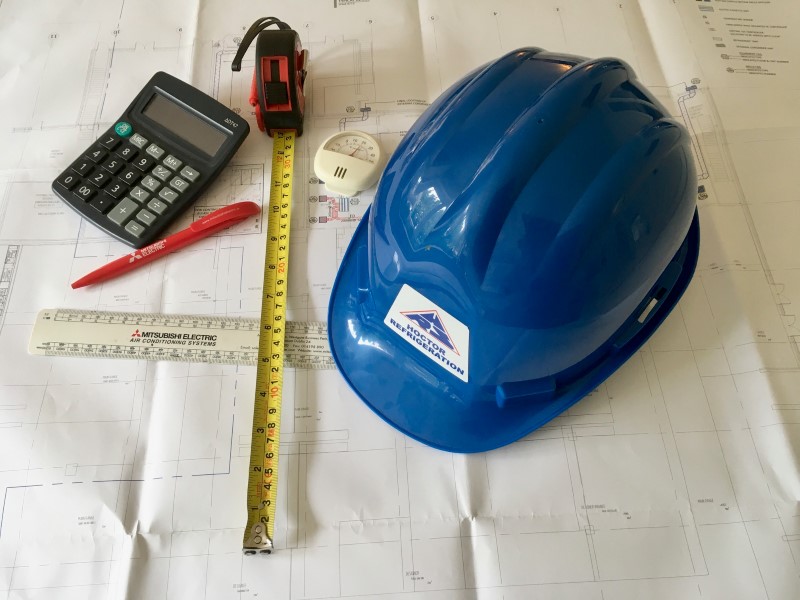
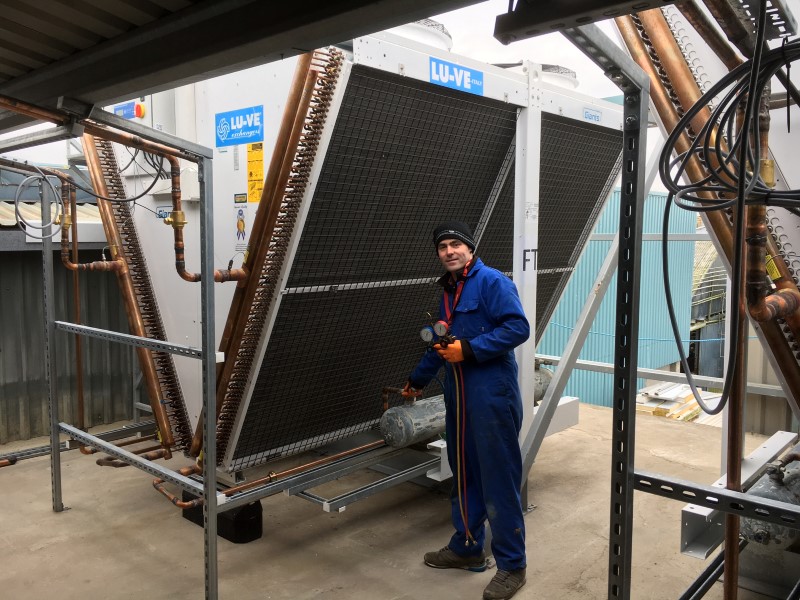
Maintenance Contract Holders
Customers with Service/Maintenance contracts are placed on a priority list for service and these customers are guaranteed a swift and efficient response.
Given the nature of our business we believe that response time is vital.
We offer same day response for all calls received by mid-day and next day response for all others, unless requested otherwise by the customer.
Recycling
Hoctor Refrigeration strive to protect the environment.
We would encourage at all times to REDUCE – REUSE – RECYCLE.
In our business a large portion of the equipment which is supplied, or removed from sites, is recyclable.
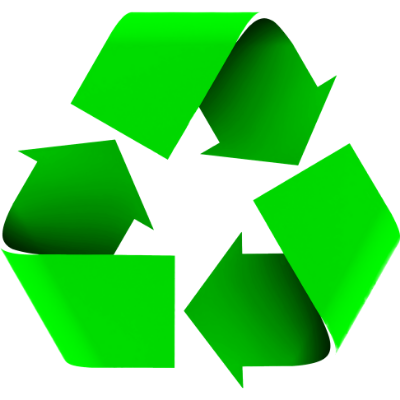